Single-Use Technology Waste in Manufacturing Operations

Single-use products used in the production of biologics provide flexibility that was unimaginable a few years ago. The implementation of single-use technology (SUT) in manufacturing operations has accelerated due to reduced risk, flexible process equipment adjustments, and lower capital cost. The widespread use of this technology has raised questions about its impact on the environment due to the shift from traditional operational utilities (heat, water, chemicals) to single-use plastic products.
The introduction of SUT in biologics production has raised questions concerning the proper handling of SUT consumables once they have been used to create valuable therapeutics1. This topic has been researched from various perspectives; research shows that SUT systems can have a lower environmental impact when compared to traditional systems, which require high-purity water and heat to clean and sterilize reusable materials1.
However, although SUT systems reduce the carbon footprint from energy use, they increase the quantity of plastic materials used. To address the plastic use, we can look at ways to minimize utilization, but ultimately there will be waste that requires disposal.
There are significant challenges for waste disposal and handling at the manufacturing plant level:
- Separation of different types of plastics (recyclable and noncompliant materials)
- Management and waste of cardboard and associated dunnage
- Development of an inactivation procedure if considered regulated medical waste (chemical or heat)
- Staging of materials as process waste in the suites and in holding areas outside of manufacturing
- Limited options for local waste collection or hauling to potential recycling facilities
Even though the handling of plastic waste is already incorporated into the typical manufacturing process, the quantity increases significantly in a manufacturing operation when SUT is implemented. What is the industry currently doing to handle this increased plastic waste and is there potential for improvement? These are the main topics that initiated this investigation by the ISPE Disposables/Single-Use Community of Practice (CoP).
A focus team in the ISPE Disposables/Single-Use CoP conducted in-depth surveys of biopharmaceutical manufacturers to assess the importance of dealing with SUT waste materials and the respondents’ sensitivity to reducing the waste’s impact on the environment. Although over 40 people responded, not all of them replied to every question. The purpose was to obtain feedback, in an area where there is none, from users to help inform others in the industry and guide future work.
SURVEY DETAILS
Size of Participating Organizations
The participants in the survey included organizations of various sizes. These organizations ranged from small firms (up to 100 employees) to larger companies (> 1,000 employees). The results were categorized in these four size segments: companies with < 100 employee, 101–300 employees, 301–1,000 employees, and > 1,000 employees.
Regions of Participating Organizations
The respondents represented companies across the globe. Although many companies operate in more than one region, respondents that identified a specific area included companies in the regions classified in Figure 1.
TOPICS DISCUSSED
The survey covered two broad areas. The first area dealt with current practices for the disposal of plastic waste. The second dealt with options for improving the outcome with the disposal of the SUT assemblies. The results shown are presented accordingly in this article.
SURVEY RESULTS
Quantity of Waste Produced
Participants were asked to estimate the total weight of the single-use assembly waste being generated at their facility. The total weight indicated greatly varied, with one-third of respondents estimating roughly 200 kilograms (kg)/month, one-third of respondents estimating up to 1,000 kg/month, and one-third of respondents representing larger users and estimating > 1,000 kg/month. The large variations seen are impacted by the size of the plant, the level of integration of single-use products, and the throughput of the single-use assembly materials.
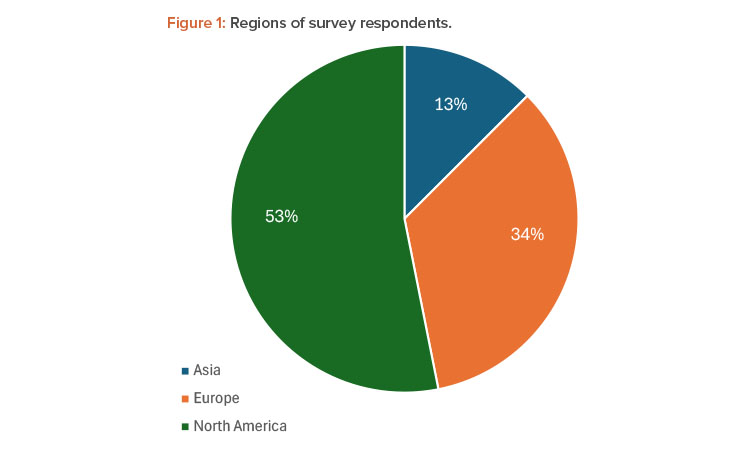
Disassembly of Single-Use Assemblies
Approximately one-third of the respondents required the disassembly of SUT items. If a facility is employing SUT recycling, it may be necessary to separate out resin materials to facilitate the sorting of different materials of construction. For those that send their single-use waste out for incineration, environmental policies can restrict the burning of some types of plastics. For 60% of respondents, laboratory and operations staff accomplish disassembly, but 40% of respondents noted their janitorial staff handle these activities.
The removal of accessory parts before disposal involves significant time and manual effort. It can also lead to environmental health and safety risks to the operators. The additional work and risk that result from disassembly, with only minimal benefits, may account for the significant percentage of respondents (63%) that simply dispose without disassembly.
The majority of what is removed from single-use assemblies appears to be metallic, including clamps and metal components. Of the respondents, 23% mention both categories (plastics and metals; multiple responses were permitted). The study did not indicate whether plastic or metal clamps were being removed before disposing of the SUT items. Clamps may be removed to facilitate the breakdown of assemblies or allow incineration/energy co-generation. Other components removed include PVC, various types of tubing (making up 17% of mentions each), and filters (12% of mentions). Additional components removed from the assemblies include sensors, pumps, and rigid plastic parts.
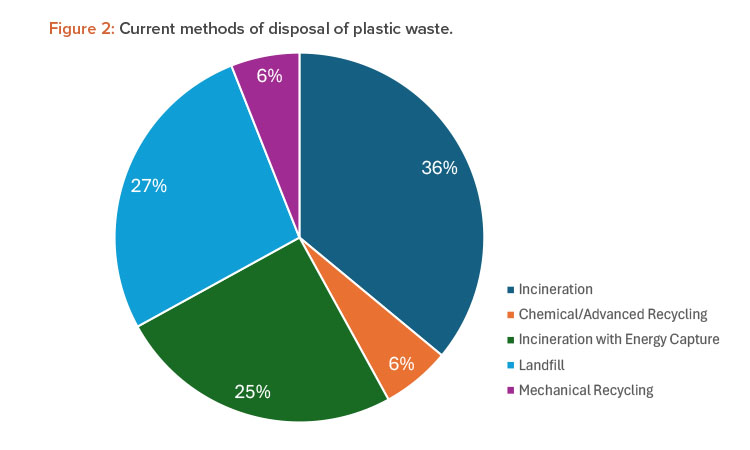
Current Disposal Practices
Over 60% of participants currently use incineration (some with energy capture) as the major disposal method for single-use assemblies. Nearly 30% of the end users dispose of SUT via traditional landfilling, and less than 15% use any form of chemical or mechanical recycling (note that multiple responses were permitted) (see Figure 2). These responses suggest that there is a large opportunity (> 45%) for alternative recycling or sustainable actions by the end users.
Handling of Biological and Regulated Medical Waste
A common challenge that end users face with biopharmaceutical waste is the mix of applications that result in both biological and regulated medical waste and nonhazardous waste. This can partially dictate some of the options for the potential recycling of plastic waste. Some organizations have established processes to handle and decontaminate waste, whereas others may not want to spend the extra time and resources to do so and dispose of the waste through regulated waste channels.
We asked survey participants if the single-use assembly waste at their facilities is considered nonhazardous or biological and regulated medical waste after use. Approximately 38% of respondents indicated that all single-use assembly waste is considered biological or regulated medical waste, 23% indicated it is all nonhazardous waste, and approximately 38% indicated they have a mix of both. For those that indicated both, nearly 50% of the waste is estimated to be nonhazardous.
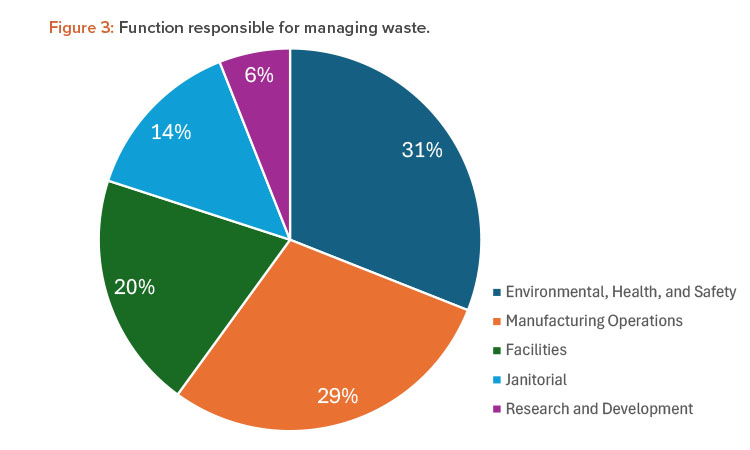
For the biological and regulated medical waste created, 41% of respondents sterilize the single-use assemblies after use. Various methods are used for decontamination, including the use of on-site heat decontamination equipment (53% of mentions), on-site chemical decontamination (33% of mentions), and third-party removal or decontamination (14% of mentions). Decontamination prior to disposal can decrease the costs to dispose the waste by reducing the need to handle it as biological or regulated medical waste. Decontamination may also offer more opportunities to recycle.
The methods used for decontamination are varied and the impact needs to be assessed on a case-by-case basis. For example, steam-based techniques are routinely used to treat single-use materials. Although additional costs are required to purchase and operate the machines, these costs are offset by the large reduction in the volume of biological and regulated medical waste. This reduces subsequent transport and processing costs and creates potential opportunities for recycling. This is an area that needs further investigation and analysis.
Function Responsible for Managing Waste
Managing waste at the site level can be complex, time intensive, and a challenge with regard to storage space, logistics flows, and safety considerations.
Waste from single-use assemblies results from at least three different areas:
- Packaging waste (polystyrene; plastic bubble wrap and film; cardboard; miscellaneous straps; and adhesive tape)
- The consumable bioprocess container or tubing set being used in the process
- Inactivated waste from decontamination, including the melted single-use assembly from heat inactivation (autoclaving), bleach use, base, or other inactivation solutions
The specific function within an organization that handles each of the previously mentioned waste streams at a typical manufacturing site can vary greatly depending on the waste stream and how the facilities’ duties are divided (see Figure 3). The survey results indicated that approximately 60% of the handling is performed by manufacturing operations and environmental, health, and safety roles—accounting for the highest level of waste management. Only 20% of the handling was performed by facilities teams, with another 20% of the handling being performed by janitorial and research and development functions.
A total of 42% of the respondents selected more than one function, showing that there is a large discrepancy on how, and by whom, waste is handled, and that there are opportunities to streamline the processes.
Increasing Process Efficiency
Many single-use advocates and end user decision-makers consider the current methods for the disposal of biological single-use assemblies to be unsustainable and less than desirable. Research has shown that most end users feel something better can and should be done 2, 3. More ecological ways exist to transfer the used products out of the production line and into a process that minimizes costs and environmental impact. The survey results confirm the generally held view that current methods are inadequate and that there is a lack of more acceptable options.
Many of the respondents, comprising organizations in all regions and of a variety of sizes, indicated that their organizations have established goals for environmental sustainability and are committed to improving their practices. (Note that more than one option could be selected.)
- Almost half (49%) have a corporate sustainability waste goal
- Nearly half (46%) have initiatives focused on reducing single-use assembly waste
- Over half (52%) have initiatives for recycling or better end-of-life management of single-use assemblies
- Approximately one-third (27%) have goals or initiatives for all three of the previously listed objectives
Improving Disposal of SUT Assemblies
The great news for the industry is that most survey respondents support becoming more actively engaged in effective end-of-life management solutions. From survey responses, the preferred methods of disposal for single-use assemblies were incineration with energy capture, mechanical recycling, and chemical recycling. (Note that more than one option could be selected.)
- 74% selected recycling, chemical, and/or mechanical
- 42% selected incineration with energy capture
- 18% selected incineration without energy capture
- 5% selected landfill
Overall, most respondents are looking to dispose of single-use assembly waste more sustainably, with chemical and mechanical recycling being top choices. There are currently limited options for recycling SUT materials, but increased use of SUT products in the industry can increase the available options.
There are potential opportunities for landfill avoidance through waste to energy (incineration), mechanical recycling (e.g., conversion to plastic lumber)4, and chemical recycling (chemical breakdown of molecules to create inputs for plastic resin manufacturing).
Recycling requires one or more steps to support rerouting waste compared to landfill disposal. However, 92% (35 of 38) of respondents indicated they are willing to take additional actions in handling single-use materials to allow for better end-of-life management. If better end-of-life management were available, approximately half of the respondents would be willing to sort packaging separately (55% of mentions), remove metal components (50% of mentions), and/or decontaminate single-use assemblies (47% of mentions).
Additionally, 42% of respondents would be willing to remove tubing from single-use assemblies. Eight percent of respondents suggested they would be willing to take the extra step to sort plastic types separately. A low percentage of respondents (8%) indicated they would not be willing to carry out any of the actions listed. Note that more than one option could be selected and 53% of respondents selected two or more options.
Most respondents would be willing to take action to handle the single-use assembly waste to enable more sustainable disposal options. Sorting of packaging materials is one of the simpler actions that could be easily adopted. Removal of specific components within the single-use assemblies requires more labor and could be more feasible if changes in product design allowed for the easy removal of specific components. Decontamination also requires more labor, but has benefits in reducing the volume of biological and regulated medical waste.
Partnering with Suppliers
Survey results suggest that product suppliers could impact end-of-life outcomes, with 64% of respondents indicating they would pay them a premium price for better end-of-life management. Figure 4 shows how much added cost the respondents that indicated they would pay a premium price would consider acceptable:
The data shows that over half of the respondents would be willing to pay a small premium for the products they purchase for more sustainable disposal options. Purchasing cost sensitivities can impact the decision to choose a more sustainable product, but looking more holistically at the total product life cycle cost may show a cost benefit if disposal impacts are reduced.
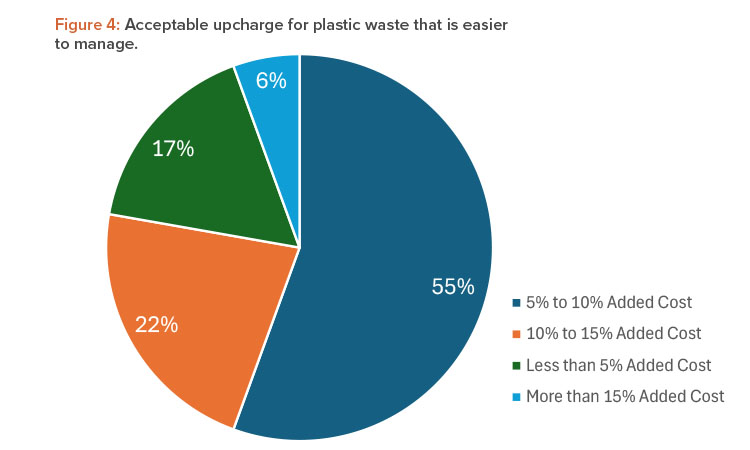
Survey participants were asked to rank various potential supplier offerings for better end-of-life management of single-use assemblies. The top three ranked options were:
- Provide a third-party recycling company that can offer recycling and transport at the same or lower cost than current disposal method
- Optimize packaging to reduce packaging waste
- Add to product cost for end-of-life management but with a more environmentally sustainable solution for disposal
If suppliers improved the single-use assembly design for better end-of-life management, most users would consider them for their processes. Eighty-five percent of respondents would consider purchasing the improved designs for new and existing processes. Of these, 59% would consider replacing assemblies for existing processes.
A majority of respondents (81%) also indicated that their organizations would dedicate additional resources to support improved end-of-life management. An additional 10 hours a week was considered acceptable for 78% of respondents. Survey respondents provided the following suggestions for how suppliers can help improve end-of-life management of single-use materials:
- Provide more information on options and approaches
- Design the assemblies to be easily disassembled
- Reduce the extent of single-use assemblies by using reusable systems
- Take back used components and systems
Other comments are aligned to approaches for recycling. This includes an increase in thermoplastics for melting and reuse and chemical and biological approaches to recycling. It is likely that the survey is self-selecting, or that those that have a strong interest in this area have responded. It is encouraging that those that did respond are keen to actively take part in improving end-of-life management.
The survey respondents all have a strong commitment to recycling using internal resources. Further, users are open to incorporating innovative designs for components and systems that ease end-of-life management.
CONCLUSION
The survey research shows that collaboration and partnerships are essential factors to improve the management of SUT waste:
- For manufacturers: Change designs to facilitate easier recycling and disassembly at end of life, optimize and reduce packaging waste, and provide end-of-life solutions.
- For end users: Dedicate resource time to decontaminate and remove parts of the single-use assemblies for recycling.
- For recyclers: Partner with suppliers to provide design recommendations for recyclable products and to conduct feasibility for current design recyclability.
Organizations aim to make their operations sustainable. However, with increased SUT use, the bioprocessing industry is worried about the management of waste and the environmental impact of single-use products. It is evident from the responses in this survey that end users feel that the current waste treatment methods are insufficient and require improvement.
The survey results provide direction that requires industry collaboration. There is a need to evaluate which of the identified solutions offers the greatest potential for improvements. In addition, we may gain insights to further solutions by observing how other industries approach the issue of SUT waste and evaluate whether there are any viable options for the biopharmaceutical industry.
Acknowledgments
Authors are members of ISPE’s Disposables/Single-Use Community of Practice Steering Committee.