FOYA Projects Embrace Innovative Sustainability Solutions
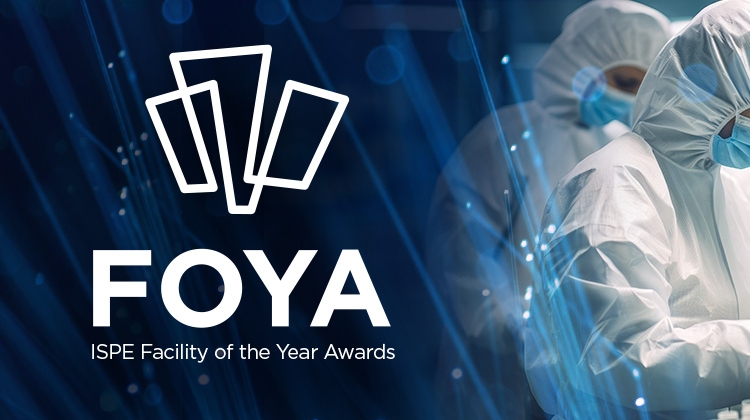
Established in 2004, the Facility of the Year Awards (FOYA) recognize state-of-the-art projects utilizing new, innovative technologies to improve the quality of products, reduce the cost of producing high-quality medicines, and demonstrate advances in project delivery.
The FOYA program provides a platform for the pharmaceutical science and manufacturing industry to showcase its accomplishments in facility design, construction, and operations while sharing the development of new applications of technology and cutting-edge approaches. In 2019, Celgene International was awarded a FOYA in Sustainability for its project La Fée Verte in Switzerland. But, as the industry became more aware of the need to design with the environment in mind, sustainability became a must-have to be considered for a FOYA. This year’s category winners are no different. Each winner incorporated sustainability design into their project and has ambitious goals to help protect our environment for the future.
Innovation: IE2B
Sustainability responsibility has always been important to Lilly. Making medicines requires the use of valuable resources including energy, water, and raw materials, and Lilly has an ambitious goal to become net zero by 2030. Innovative engineering design plays a significant part in Lilly’s sustainability journey. Decarbonization needs capital investment to replace established high carbon footprint manufacturing platforms and technology with low carbon footprint technologies and efficient unit operation design. Having a sustainability focus in the early design phase of a new facility or project can yield significant benefits—equipment and technology choice is correct from the beginning versus an expensive retrofit of equipment in an already operating plant. Deliberate forward thinking decisions can ensure smart design to optimize energy usage, water usage, and raw material usage. This approach can yield significant sustainability advantages but also may yield lower operational costs and efficiency for manufacturing plants, creating a potential win-win.
Sustainability was a significant consideration when Eli Lilly Kinsale Limited was designing its new synthetic peptide manufacturing facility (IE2b) located in Kinsale, Ireland. The new IE2b facility uses a hybrid manufacturing platform—liquid-phase peptide synthesis/solid-phase peptide synthesis (LPPS/SPPS). This combines the traditional approaches to synthetic peptide production using SPPS to manufacture high-purity preassembled peptide fragments. This is combined with coupling the fragments via LPPS using continuous processing technology.
The process is designed to be efficient with many of the continuous processing steps, producing conversion yields of over 98%. This ensures minimal waste of input raw materials. The telescoped nature (running steps one to three as one continuous process) of the design eliminates the need for multiple setups and cleanups between each process step, which reduces the need for additional cleaning solvents and cleaning materials.
Other highlights include:
- The integrated modular cleaning and maintenance strategy has reduced cleaning timelines by approximately 25%.
- The IE2b peptide hybrid manufacturing process produces 20% less solvent waste per month compared to a typical batch-based small-molecule process.
- The telescoped design of the process eliminates the need for individual step cleanups, which equates to an annual reduction of over 100 metric tons of solvent needed for cleaning activities when compared with a traditional three-step batch-based equivalent process.
Lilly Kinsale also installed a 5.6-megawatt (MW) commercial solar farm adjacent to the Kinsale manufacturing site. This solar farm contributes to approximately 15% of the IE2b facility power needs and supplements the power needs of the rest of the Kinsale site.
Project Execution: TUAS 2
Pfizer Asia Pacific Manufacturing Ltd.’s Tuas 2 facility in Tuas, Singapore, will produce active pharmaceutical ingredients (APIs) for a portfolio of medicines across a range of therapeutic areas such as oncology, autoimmune disease, cardiology, and antibiotics. Pfizer identified and implemented over 184 sustainability improvement opportunities at the site, including:
- Installing a roof-mounted photovoltaic panel system capable of meeting all the site’s nonprocessing electricity needs
- Replacing cabled street lighting with LED solar-powered street lighting and maximizing natural lighting inside
- Providing better bus, bicycle, and electric car facilities
- Using native and drought-resistant plants in landscaping
- Improving heating, ventilation, and air conditioning (HVAC) systems by using recirculation and heat recovery systems
- Improving the endotoxin water system by challenging end user loads and equipment and system needs
- Reducing the piping requirement, equipment sizes, and loop sizes of the water system, and specifying a reverse osmosis system with very low reject water over variable frequency drive and demand control
- Installing electronically commutated fan walls where atmosphere explosible requirements and duct pressures allowed: this space-saving solution improved specific fan power with a greater level of redundancy
As the industry became more aware of the need to design with the environment in mind, sustainability became a must-have to be considered for a FOYA. Each category winner incorporated sustainability design into their project and has ambitious goals to help protect our environment for the future.
It is anticipated that all the sustainability improvements could lead to an annual energy savings of 80.5 terajoules, which is an incredible 31% improvement from the initial concept design.
Operations – Facility Fit: Takeda’s Manufacturing Site Linz, Austria
The focus of Takeda’s Manufacturing Site in Linz, Austria, is the production of biologics for the treatment of chronic inflammatory bowel diseases in various forms. Takeda managed to reduce the process performance qualification time by 50% for the new prefilled syringe filling line. Once fully operational, the Linz site will fill and finish 70% of the global demand for this product.
Learn about the latest advancements in manufacturing and cutting-edge digital advancements including sustainability initiatives at the 2025 Facilities of the Future Conference 27–28 January in San Francisco, California, US, and Virtual.
With a strong focus on sustainability, Takeda installed about 20 new freezers to store the active ingredient, shortening global supply chains. The team made a notable transition to non-multipack packaging and up to 70% of cartons and 50% of leaflets are anticipated to be saved with this change. In addition to reducing waste, these
steps also reduce Takeda’s carbon footprint, aligning with their sustainability goals. Takeda continues to evaluate and implement innovative sustainable solutions, such as a renewable energy supply, along the entire value chain.
Social Impact: UK4
As part of its business strategy, Chugai Pharma Manufacturing Co., Ltd. has placed sustainability at the heart of its business activities and aims to be a global role model. UK4, their new 40,000-square-foot biological drug substance manufacturing facility in Tokyo, Japan, was specifically designed and built for the manufacture of early-stage investigational medicinal products under a “Three Zeros for Sustainable Development” concept. UK4 employed innovative solutions to achieve the Three Zeros goal.
- Zero halogenated hydrocarbons: They used naturally occurring coolants like NH3 and CO2 instead of the traditional halogenated hydrocarbons to achieve the goal of zero halogenated hydrocarbons. The cooling source is provided by ammonia chillers, whereas the heating source is provided by CO2 heat pumps.
- Zero natural gas: To avoid using natural gas, they installed electric boilers to supply the needed steam. This was possible, in great part, due to several design decisions that resulted in reduced steam demand. These included using CO2 pumps as heat sources, increasing the use of single-use equipment, eliminating the need for cleaning, and adopting a membrane-based process water system (cold water for injection system) instead of distillation-based equipment.
- Zero CO2 in non-GMP areas: To achieve the last goal of zero CO2 in non-GMP areas, UK4 implemented several solutions to reduce energy consumption and to generate what was needed using renewable sources. Solar panels were installed on the roof and integrated into the facade of the building. The northern facade featured louvers to block direct sunlight and redirect natural light into the clean rooms. Several additional energy management solutions were implemented across the site, including adjustments to room air changes based on load and lighting control based on occupancy.
Finally, a water reuse strategy was implemented that included recovering rainwater and HVAC condensate to reduce water consumption and the energy needed to produce it. All of this is monitored by a centralized energy and environmental monitoring system to ensure proper operation and to validate efficiency.
FOYA Honorable Mention: United Therapeutics’ Research Triangle Park Site
United Therapeutics needed to expand their warehousing and logistics capabilities to support their growing operations due to the anticipated FDA approval of Tyvaso DPI, a new formulation and inhalation device for inhaled treprostinil and the only dry powder inhaler approved by the FDA for use in pulmonary arterial hypertension and pulmonary arterial hypertension with interstitial lung disease (PH-ILD).
They identified site carbon and net zero as two sustainability requirements for the project and adopted the mindset that they could develop life-saving medicines for patients without harming the planet. The new facility is unmatched when it comes to environmental responsibility for a current GMP warehouse and operations center and is designed to be able to maintain operation even during electrical grid outages.
The facility incorporates several technological innovations that contribute to its site net- and carbon-zero goals, such as passive and active energy reduction strategies, rooftop photovoltaic arrays, a geothermal exchange system, microgrid technology, and a battery backup system (Tesla Megapacks). These systems allow the facility to use renewable energy, push excess energy back to the grid, and maintain a stable current GMP environment for the ambient and cold storage areas. The project is expected to receive LEED Gold, LEED Zero Energy, LEED Zero Carbon, and Energy Star certifications.
To minimize the ecological impact of the project, United Therapeutics built the new facility on an existing underutilized soccer field on their Research Triangle Park campus in Raleigh, North Carolina. Locating the facility on the corner of their campus adjacent to their new site net-zero childcare center enabled them to avoid clear-cutting the remaining wooded area on campus and provided for the adaptive reuse of the existing fieldhouse.
Sustainability achievements included:
- All-electric system design to facilitate on-site energy offset with renewables
- Low-energy design without impact on the program needs of the current GMP facility
- A ground-coupled geothermal heating and cooling system generating chilled water and heating water for the current GMP warehouse
- On-site zero energy, producing as much or more energy from renewables as is consumed
- On-site zero carbon, offsetting all carbon emissions associated with energy for typical building operations with on-site renewables
- Two Tesla Megapacks of battery energy storage systems with a total of 6.2 megawatt-hour (MWH) of backup power. This supports 8, 24, and 48 hours of code-required loads, ambient storage, and cold storage without any recharging
United Therapeutics’ facility is the first of its kind in the world to deliver this performance to a current GMP operations and logistics facility. With the completion of the new warehouse, United Therapeutics has completed four site net-zero energy projects and has numerous LEED-certified projects including the Unisphere, their award-winning headquarters in Silver Spring, Maryland, which is the US’s largest site net-zero urban office building.
FOYA Honorable Mention: Zydus Pharmaceuticals’ Gujarat Site
Zydus Pharmaceuticals’ new greenfield cutting-edge oral solid dosage (OSD) manufacturing facility located in Gujarat, India, is dedicated to manufacturing OSD products. Zydus as an organization believes in sustainable inclusive growth where not only the organization but also the stakeholders’ interests and well-being are prioritized. To that end, the following are a few of the measures they took with the new facility:
- Initiated a watershed development project in water-stressed areas of Gujarat including several interventions such as developing village ponds, farm ponds, rainwater injection bore wells, and check dams through which runoff rainwater is stored and harvested in aquifers. The organization is trying to harvest about 2 billion liters of water in three years through these interventions.
- Extensive planting through a speedball campaign
- Focused water and energy conservation activities including recycling wastewater through robust treatment using energy-efficient motors, motion sensors, LED lights, and green fuel for boilers
- Recycling 420 metric tons of plastic waste generated from its operations as extended producer responsibility
- Sending more than 2,700 metric tons of hazardous waste with high-calorific value to the cement industry for co-processing during the 2022–2023 financial year
Additionally, the site environmental management system includes infrastructure like a wastewater treatment plant, dedicated stormwater drains, hazardous waste storage facility, and emission control equipment. Process vents are equipped with HEPA filters and the performance of the pollution control equipment is monitored on a regular basis.
Learn more about the 2024 FOYA category winners, including the 2024 FOYA winner