Embracing the Human Side of Manufacturing

For companies focused on producing lifesaving treatments, the positive effects of employee health, well-being, and satisfaction can be easily overlooked, but those positive effects are real. An investment in people results in better research, testing, and manufacturing processes, which leads to more efficient delivery of therapies and treatment to patients worldwide.
In the biopharmaceutical industry, it is expected that corporations emphasize the primacy of the patient in their mission statements, reflecting the core focus of the field. However, it is less common to observe one of the world’s largest pharmaceutical manufacturing facilities placing significant emphasis on the health and satisfaction of its employees. This focus on employee well-being plays a crucial role in the effective delivery of therapies to patients.
Embracing the fundamental idea that there is an explicit connection between the well-being of employees and the health of the patients it serves, Takeda planned its Georgia Manufacturing Facility with a human-centered approach. The 1.1-million-square-foot facility was deliberately designed to support employee health, well-being, and resiliency.
In planning the facility, Takeda viewed these ideas not as additional benefits but as key factors to increase efficiency and efficacy and ultimately accomplish its goal of delivering plasma-derived therapies for people living with serious and complex health conditions.
With over 1,300 full-time employees, the facility is arranged to encourage collaboration and foster human connections and relationships. Amenities such as on-site nurses and sports courts that support wellness, paired with a design that reflects a culture of transparency, make clear the intention to draw a bright line connecting the health of Takeda’s employees and the health of the patients they serve.
Human-Centric Design
The initial planning and design of a successful pharmaceutical manufacturing facility includes many considerations, such as maximizing production and volume, process and environmental controls, and cleanroom classifications, to name a few. For large manufacturing facilities such as this one, the human experience is often overshadowed by the focus on production yield and the bottom line.
When Takeda engaged Flad Architects to master plan the facility, they considered the project’s ability to create a positive impact on both patients and Takeda employees. From the employee perspective, the key objectives for the project were attracting and retaining talent; improving employee health; promoting diversity, equity, and inclusion; and fostering lifelong learning and growth. To accomplish these objectives, Takeda placed a major emphasis on human-centric factors and how the building occupants would experience the space (see Figure 1).
This focus informed decisions for all aspects of the buildings at all phases of the project, from site selection and early concepts through final design, construction, and occupancy. The human-centric focus encompassed not only the administration and collaboration spaces, but also, and more importantly, manufacturing and manufacturing support spaces.
Supporting health and well-being includes physical considerations such as opportunities for physical activity in daily work life, air quality, temperature, natural light, glare control, and noise level. It also includes less tangible — but just as important — factors such as a sense of community and a connection to both the organization’s mission and nature.
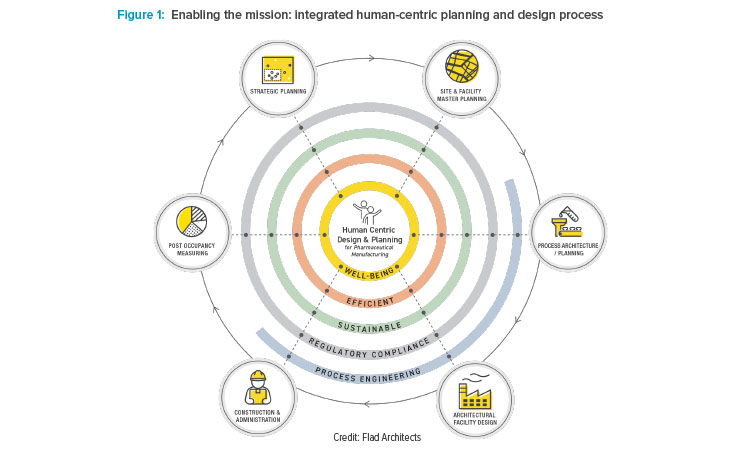
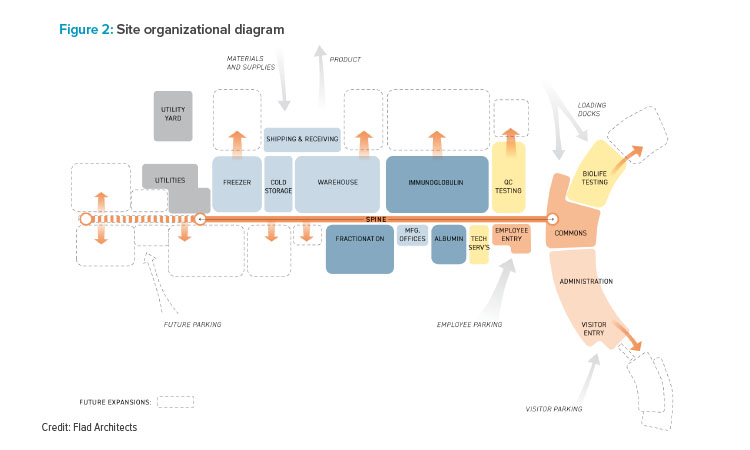
The site’s paramount purpose is the processing of human plasma and fractionation of plasma proteins to yield albumin and immunoglobulin. Plasma fractionation is the first step of the manufacturing process and the second largest user of materials coming from the warehouse, after the immunoglobulin process, filling and packaging operations. Therefore, the four-level fractionation space, comprising 187,000 square feet, is located directly across from the warehouse (see Figure 2). The albumin operations, located in a four-story building, house the equipment needed to purify specific proteins from the fractionation area. This includes buffer solution vessels, centrifuges, and filter presses used to separate distinct proteins from human plasma.
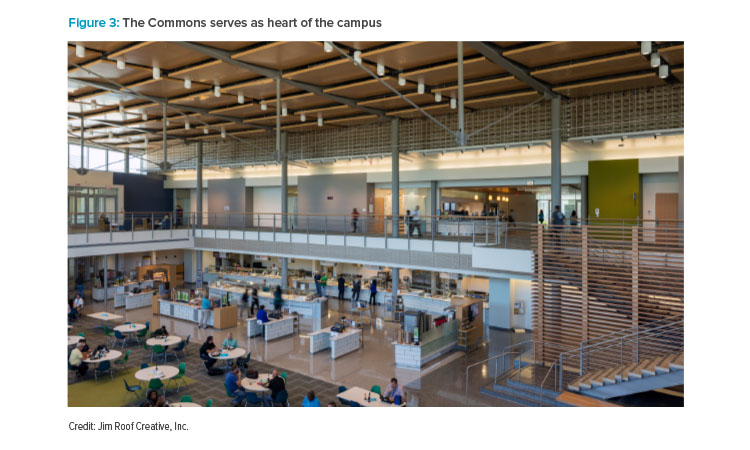
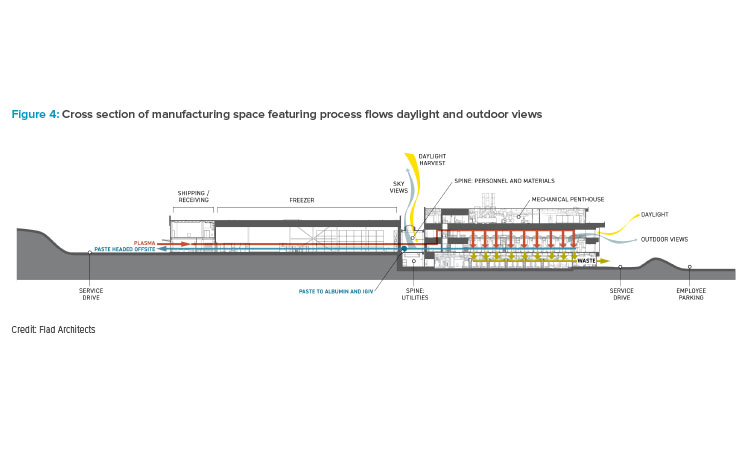
To achieve optimal efficiency among each of the program elements, the design team considered the most logical flow of materials and product, as well as how people would move through the facility. Extra care was taken with the placement of primary and support areas, maintaining the most vital adjacencies of various production functions.
To reach human-centric planning goals such as Takeda’s requires thoughtful consideration at every stage of the project. Starting with initial planning, the focus on the idea of engaging employees and collaboration is evident in the floor plans. The design team considered how and where employees would interact with each other; and what they should see, feel, and experience. This includes access to natural light and views to the outside as well as the length of time to de-gown and move to the cafeteria, restrooms, or parking lot.
In addition to situating the manufacturing offices centrally within the process areas, the plan positions the units that generate the most samples and have the most employees as close to the quality control labs as possible. The Commons (see Figure 3), a two-story space that acts as the facility’s “Times Square,” is the heart of the campus. It’s an active area where people pass through from all directions. The cafeteria is located on the ground floor with a 360-degree balcony overlooking it. A coffee corner, fitness center, sports courts, and shared computer stations are located just off the balcony area.
This series of conscious decisions allowed for the creation and optimal location of the heart of the campus, where all employees can share a common experience, filled with natural light and views. This provides ample opportunities to collaborate and build community as people dedicated to improving the health of patients.
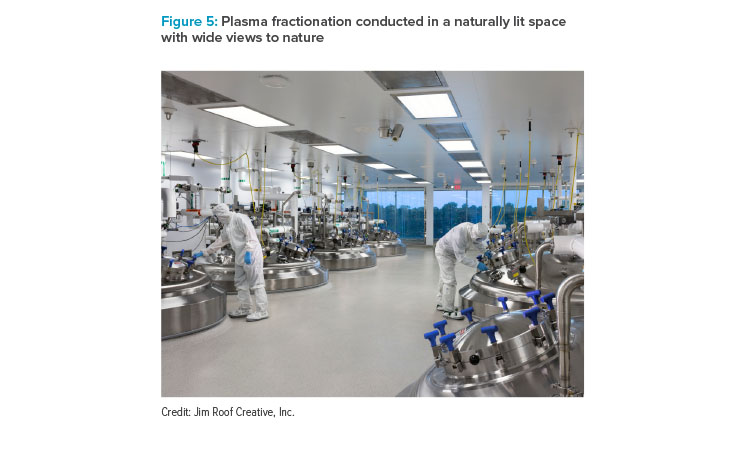
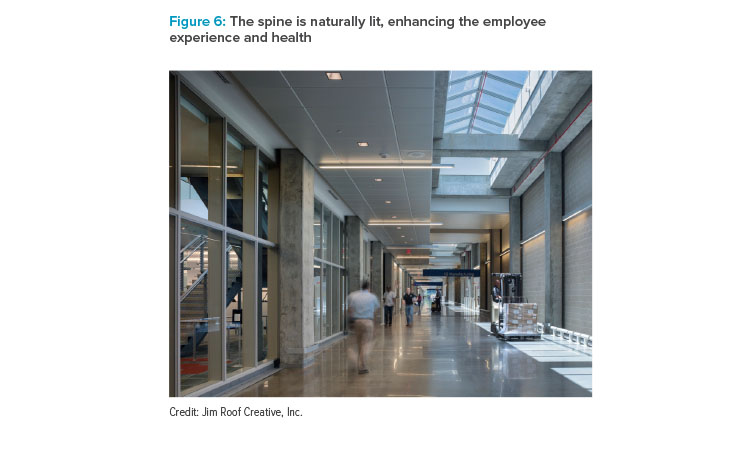
Design to Support Health and Well-Being
Most employees in manufacturing spaces are physically active throughout the day, doing important work that requires focus. For the sake of safety and to avoid contamination, these workers are often wearing personal protective equipment and, in a typical manufacturing plant, may find themselves in an isolated, contained working space. To help these employees remain inspired and engaged, the design team focused on providing access to daylight and views to the outside and adjacent spaces within the building. Exposure to natural light and the outdoors has been proven to significantly improve mood and reduce stress, with the added benefit of boosting productivity and cognitive function. The building design maximizes every opportunity to provide natural light to employees using large windows and glass walls, including floor-to-ceiling windows in some areas. This includes admitting natural light into (and views out from) even the cleanest and most regulated cGMP manufacturing suites (see Figures 4 and 5). In addition to boosting employee well-being, the extensive use of glass also provides a literal window into the facility’s intricate processes for the benefit of passing employees, visitors, and regulators to the facility.
For the central spine, which runs between warehouses, freezers, and manufacturing spaces, windows to the exterior were not an option. Instead, it features a skylight system to infuse natural light (see Figures 4 and 6). This 400-meter corridor spanning the length of the facility serves as the link that connects all operational and administrative spaces. The lower level of the spine carries all the major utilities for the campus. Along the upper-story spine, the controlled not classified (CNC) offices are adjacent to the manufacturing spaces that they serve. Central placement of CNC offices allows members of the different manufacturing support teams to collaborate and build relationships that could potentially lead to new ideas and process improvements and innovations.
Focusing on physical transparency also supports a culture of transparency. Providing views into the functional areas promotes a sense of community and enables passive supervision and communication as well as improved employee safety. Transparent designs allow management and staff to visually connect, verify safety, and rapidly identify and respond to any issues. It allows each team member to pursue their individual tasks while being visually connected to the overall team. With functional areas exposed to outside views without the need to gown or de-gown, the transparency also facilitates regulatory inspections with minimal disruption to ongoing operations.1
Enabling Physical Health: Stairs and Interactive Spaces
Although occupants of the administrative spaces may not be on their feet physically exerting energy all day, the negative health effects from sitting for long periods of time are well documented. People with inactive lifestyles are at higher risk of hypertension, high blood sugar, and obesity,2 so the building design incorporates “design-led intervention” strategies3 to encourage activity. Research published in the Journal of the Royal Society of Medicine indicates these “design-led interventions can make better (healthier) choices easier or constrain (less healthy) behaviors by making certain actions more difficult.”3
Stairs and interactive spaces that minimize the use of elevators are strategically placed throughout the facility to help promote physical activity, movement, and interaction. In addition to these collaboration nodes, walking paths and a wide range of workspaces encourage people to get up from their desks and move around. The design also provides the opportunity to tailor their work to the type of environment that they need, whether it’s a private, quiet, or collaborative space.
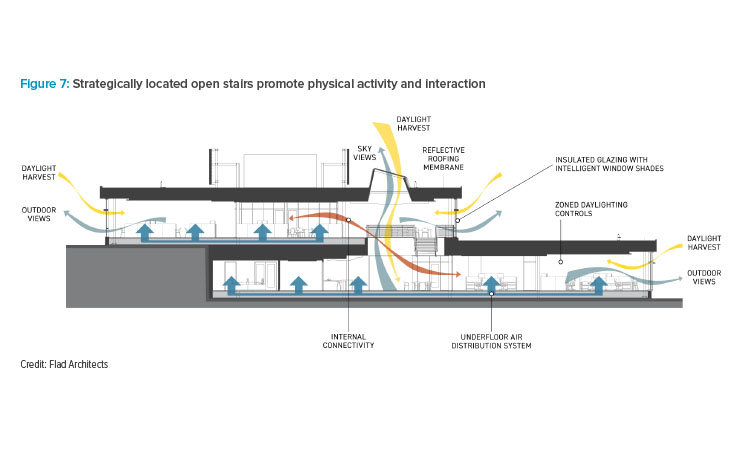
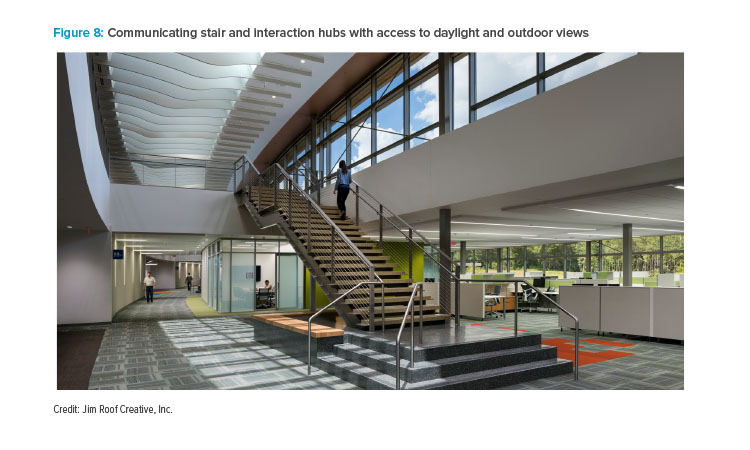
The two levels of the administrative wing (see Figure 7) are fully interconnected by three light-filled atriums that include communicating stairs (see Figure 8), providing connectivity to an already open, collaborative, and transparent office environment. These elements that encourage physical movement and interaction are congruent with design recommendations based on recent research on well-being and its relationship to health.4 Additional features were implemented to maximize air quality and comfort, such as zoned lighting controls, intelligent shading devices that improve light quality and reduce glare, and an underfloor air distribution system with localized controls to optimize thermal comfort.
Post-Pandemic Additions
During the pandemic, Takeda switched to a hybrid work model, with employees going into the facility two days a week. In 2023, employees began returning to the office more frequently, and by fall of 2024, the facility had returned to a full-time in-person workplace.
The quality of the space in the facility, with its human-centered design, was key in the success of the return-to-work strategy after the pandemic. In addition, Takeda implemented a number of additional amenity spaces including tennis and pickleball courts, ping pong tables, a barbecue smoker, and a giant TV wall. The TV is used to build collaboration and culture by displaying employees of the month, pets of the month, and information about upcoming events. Other additions include an on-site recycling plant that supports an ambitious zero-waste-to-landfill goal and a patient mural, reinforcing the impact of the work done at the manufacturing facility.
The Ultimate Connection: Building Design – Employee Well-Being– Productivity
Do happier, healthier employees do better work? Two studies out of the United Kingdom suggest they do. Economists at Warwick University found a causal link between human well-being and performance: three different experiments showed a 12% increase in productivity by happy workers against a 10% decrease by unhappy workers.5 Additional research performed by University College London found “a clear, positive, and statistically significant relationship between the average level of job satisfaction at the workplace and workplace performance.”6 Warwick researchers also noted that happy workers proved to be more effective collaborators, and there is evidence to suggest that a more collaborative environment leads to greater work satisfaction.
A post occupancy survey conducted by Takeda and Flad Architects found that the majority of employees in the Covington facility are satisfied with building attributes. A 15-question survey was sent out to employees to understand the impact of the facility on employees’ overall wellness. The survey had a 60% response rate.
Asked to rate their level of satisfaction of building attributes on a scale from one to five, with one representing very dissatisfied and five representing very satisfied, employees gave “access to natural light and views” an average rating of 4.38. For “overall visual connections between spaces,” the average rating was 4.12, and “accessibility to co-workers” received an average rating of 4.09. Over 55% of respondents said the design of the new environment positively contributed to their overall job satisfaction. Meanwhile, 70% of respondents said they use the open collaborative spaces at least once a week. Another 67% said they use those spaces multiple times a week.
Prospective hires in Georgia have demonstrated the facility’s value as a magnet for recruitment. During hiring, participants in a recruiting program are nine times more likely to return after pre-assessment testing when the testing was held inside the Takeda Covington facility than when the testing was held at nearby facilities operated by Takeda’s partnering agency.
Among the many benefits that accrue to businesses that invest in employee satisfaction are gains in yields, a heightened ability to spot trends and potential problems, and more effective processes for maintaining quality—which can help, for example, attain US Food and Drug Administration approvals. Taken together, these are bottom-line benefits that add up to an ability to meet market demand more quickly. Links between the quality of an environment and the health of the people within is being researched by the International WELL Building Institute (IWBI). Viewing buildings “as a platform for public health intervention...and recognizing the importance of a data-driven approach,”7 IWBI is hoping to further establish what Takeda and others have begun to see: the clear connections between employee health and the health of patients.
Conclusion
For companies focused on producing lifesaving treatments—a process in which protecting against waste, controlling capital expenditures, and maximizing operational efficiency are a must—the potential for the positive effects of employee satisfaction can be easily overlooked. However, those positive effects are real. Investing in workers makes them better collaborators, problem-anticipators, and problem-solvers. An investment in people results in better research, testing, and manufacturing processes. That, in turn, leads to a greater impact with more efficient delivery of therapies and treatment to patients worldwide.