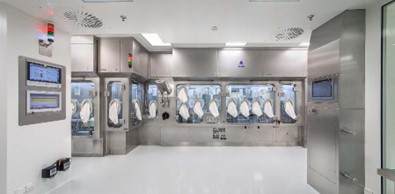
Barrier System with isolators
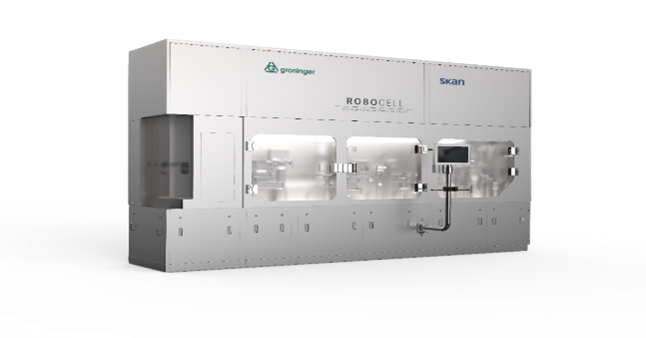
Fully gloveless Robotic Filling Line
Special focus of the completely revised Annex 1 is the application of the Quality Risk Management methodology to manufacturing, especially to the Contamination Control Strategy, the technical environment for aseptic filling, the technical conditions for clean utilities, especially for the production and storage distribution of Water for Injection. Barrier systems as RABS and isolators are recommended to be used for the manufacturing process and these two technics have been put in different clauses for each requirement, as these systems are different. .
Now the real work starts, in the center of discussion are PUPSIT = Pre Use Post Sterilisation Integrity Testing of filters, the implementation of Barrier systems based on "appropriate technologies“ and sterilization of all parts having contact with the product.
Regarding "appropriate technologies“ Annex 1 states:
"facility, equipment and process should be appropriately designed, qualified and/or validated and where applicable, subjected to ongoing verification according to the relevant sections of the GMP guide. The use of appropriate technologies (e.g. Restricted Access barrier Systems (RABS), isolators, robotic systems, rapid/alternative methods and continuous monitoring systems) should be considered to increase the protection of the product from potential extraneous sources of endotoxin/pyrogen, particulate and microbial contamination such as personnel, materials and the surrounding environment, and assist in the rapid detection of potential contaminants in the environment and the product ..... any alternative approaches to the use of RABS or isolators should be justified.“
Furthermore the H2O2 bio-decontamination is now mentioned in the Annex 1 :
"where fumigation or vapor disinfection (e.g. vapor phase Hydrogen Peroxide) of cleanrooms or associated surfaces are used, the effectiveness of any fumigation agent and dispersion system should be understood and validated“
Vaporized or nebulized Hydrogen Peroxide is widely used and accepted in aseptic manufacturing and the focus is on technology and the validation of the decontamination cycle within defined parameters.
Requirements for direct or indirect product contact parts :
"For aspetic processes, direct and indirect product contact parts should be sterilized. Direct product contact parts are those that the product passes through, such as filling needles or pumps.“
Overall, the new Annex 1 is considered as a step ahead vs. product and patient safety, is representing technical challenges for the implementation period, right now in the light of availability of technical material in the supply chains worldwide. Moreover the term „appropriate technologies“ will drive technological developments. Where new equipment will be needed and delivery time exceed the one implementation period, companies will have to prepare projects with time schedule starting the work in the one year of implementation and comply with their project schedule. However it is not needed to establish complete new facilities; it depends how the upgrade of existing facilities to Barrier Systems can be done efficiently and effectively.
ISPE’s experts in our membership will have the chance to demonstrate ways to upgrade aged facilities and to show the financial comparison between upgrade and complete new investment.
Another focus in ISPE’s conferences will certainly be first experiences from ongoing GMP inspections, and to learn how interpretation of the new Annex 1 is done by the inspectors across the agencies.
Last but not least there will be discussions and panels to discuss implementation timelines, where are the main bottlenecks and chances, where to start and what are the factors of success.
During the 2022 ISPE Pharma 4.0™ and Annex 1 Conference, taking place 7-8 December in Vienna, Austria, there will be considerations on how digital transformation can support and accelerate the implementation of the new Annex 1, as the basic philosophy of the new Annex 1 is more automation and separation from operators from aseptic processing and direct product contact.
Join us at the conference to take an in-depth look at this timely topic during sessions under Track 1: Annex 1 - Regulatory and Manufacturing Compliance and Track 3: How to Maximise Productivity by Using Closed Systems and Disposables: Annex 1.
Explore Agenda & Register